Costing more per watt of electricity generated than wind power, solar panels have no moving parts and a lifetime of 30-40 years making them ideal for professional installation with virtually no maintenance required by the homeowner.
Crystalline and Amorphous Solar Panels
Their are two main types of solar panel: crystalline and amorphous. In both cases the key ingredient is silicon. Amorphous panels are typically cheaper to manufacture (and purchase), less susceptible to breakage, and use less silicon, however their power output is typically lower than crystalline panels meaning that an amorphous solar installation would take up a larger area than a similarly power-rated crystalline installation.
Amorphous solar panels deteriorate faster than crystalline solar panels and so their power output will fall more quickly during the years of use, but they cope better with partial solar panel shading.
What is Silicon
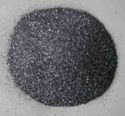
Silicon (Si) is an abundant non-metallic chemical element which makes up almost 30% of the earth’s crust and is the 7th most common element in the Universe. Silicon has two forms – amorphous(brown), and crystalline (dark).
Crystalline Solar Panel Manufacture
To make the solar cells which make up a crystalline solar panel, crystalline silicon is sliced into thin disks (aka wafers) a few millimeters thick or thinner. These are then cut to shape, polished, and any holes filled in to make the finished silicon wafer uniform.
In order to generate electricity, dopants (contaminants) have to be added to the pure silicon wafer. Typically a layer of phosphorous is coated onto the wafer and the surface is heated. Phosphorous atoms then diffuse throughout the silicon wafer contaminating it as required.
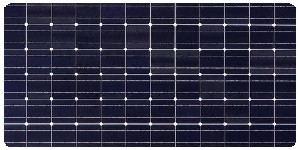
The doped silicon wafers are then aligned together to make up a solar cell, and the solar cells are arranged on a backing panel to make a solar panel (or module). Conductive metal strips are fixed to the sunward face of each solar cell (pictured below).
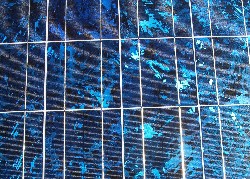
Finally a layer of glass is glued over the top of the collection of solar cells to provide protection from the elements while still permitting sunlight to pass through to the completed crystalline solar module.
Monocrystalline vs Polycrystalline
Note that there are two diffent types of crystalline solar cell – monocrystalline and polycrystalline. A monocrystalline cell is made from a single silicon crystal whereas a polycrystalline cell is made from multiple crystals. Growing a large crystal takes longer and costs more money than growing smaller crystals, so monocrystalline solar panels are usually more expensive than polycrystalline, but monocrystalline cells are more uniform and therefore more efficient.
To tell the difference between the two types of solar cell, look at the colour and shape of the cells. A monocrystalline solar panel will be black in colour whereas a polycrystalline panel will have a distinctive dark blue hue to it. Years ago monocrystalline cells were circular (as the crystal was grown into a cylindrical block), but now they are typically square with the corners chopped off. Polycrystalline solar cells are typically square with corners.
With recent advances in solar cell manufacturing, a well made polycrystalline solar cell can be much more efficient than a poorly made monocrystalline cell, so the overall quality of the solar cells and solar panel overall are more important when choosing solar panels to purchase than whether the chemisty of cells is mono- or poly- crystalline.
Amorphous Solar Panel Manufacture
Unlike crystalline solar panels, amorphous panels are not made up of a collection of interconnected solar cells manufactured from expensive crystalline silicon. Instead a very thin homogenous layer of silicon atoms and dopants is simply sprayed onto a backing material – typically glass or metal, but also on plastic surfaces to make flexible solar panels, or on roofing tiles to make solar roof tiles. The silicon layer produced can be 100 times thinner than the silicon wafers in a typical crystalline solar cell greatly reducing material costs and therefore the cost of amorphous solar panels relative to crystalline panels.
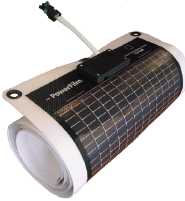
An entire solar module is made in one go, so manufacturing costs are reduced by a) not having the expense of making silicon wafers, and b) the simplicity of assembly.
Amorphous solar panel manufacture only really kicked off in the 1970’s and many experts see future developments in amorphous panels as key to continuing to bring down the costs of solar power.
Multi-junction solar cells for example are a recent development in amorphous solar technology using multiple thin layers of doped silicon to capture energy across the whole light spectrum. Multi-junction cells are the most efficient solar cells being manufactured today.